di Joannes Vermorel, Ottobre 2014Il metodo scorta massima (max) e scorta minima (min) è un meccanismo di riordino di base, supportato da molti ERP e altri software di gestione del magazzino. Il valore "Min" rappresenta il livello di scorte che, una volta raggiunto, innesca un nuovo ordine. Il valore "Max", invece, rappresenta il livello di scorte che si intende raggiungere con il nuovo ordine. La differenza tra Max e Min è spesso interpretata come il
lotto economico, o EOQ (Economic Order Quantity). Se la pianificazione delle scorte con il metodo Min/Max è piuttosto grossolana, le sue impostazioni possono essere regolate in modo dinamico per offrire migliori prestazioni in termini di gestione del magazzino.
Breve excursus storico
Il metodo Min/Max è stato uno dei primi
metodi automatici di riapprovvigionamento del magazzino a essere usati nei software di gestione del magazzino. Il pregio più evidente di questo metodo è l'estrema semplicità con cui può essere implementato.
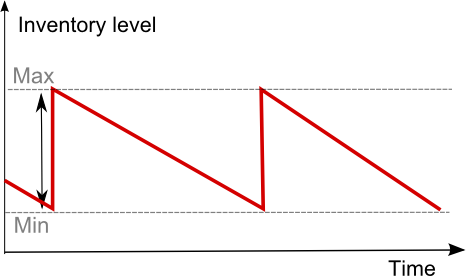
Questo metodo monitora l'attuale livello totale di scorte, che generalmente è dato dalla somma delle scorte disponibili più le scorte in corso d'ordine per ogni
SKU. Quando le scorte totali raggiungono il valore Min, viene avviata una procedura di riordino. Il quantitativo di riordino deve far sì che il livello totale delle scorte raggiunga il valore Max. Pertanto, il quantitativo di riordino è la differenza tra Max e Min (Max meno Min).
Nella versione originale, il metodo Min/Max doveva essere un metodo piuttosto statico di controllo delle scorte, in cui i valori Min e Max andavano modificati non più di qualche volta l'anno. Spesso si ricorreva all'
analisi ABC per convogliare l'attenzione delle aziende verso i prodotti "A", tradizionalmente più importanti rispetto ai prodotti "B" o "C".
Regolare le impostazioni Min/Max
Ogni azienda che intenda ottimizzare le proprie scorte deve confrontarsi con il fatto che i software di gestione del magazzino non sempre dispongono di una logica predittiva avanzata che adatti continuamente i valori Min e Max in modo automatico. Il problema, tuttavia, non è il metodo in sé: se, infatti, un altro software di ottimizzazione delle scorte fosse in grado di sovrascrivere giornalmente i valori Min e Max di ogni SKU, allora qualsiasi metodo di controllo delle scorte potrebbe essere considerato accettabile.
Per consentire a questi software di agire in tal senso e sostituire il metodo Min/Max del software principale, possiamo procedere in questo modo:
- quando non sono previsti riordini (secondo il software di ottimizzazione delle scorte in uso), la quantità Min deve essere impostata a zero o anche a -1, per evitare che un ordine venga emesso comunque;
- quando è necessario un riordino di un quantitativo X, ipotizzando che le scorte totali siano pari a S, sia il valore Min che il valore Max devono essere impostati a X+S.
Seguendo queste regole, il comportamento "di default" del metodo Min/Max, che consiste nel
riordinare fino a raggiungere il livello Max, sarà esattamente quello indicato dal software di ottimizzazione delle scorte che accompagna il software di gestione del magazzino.
Usare due software distinti, uno per l'ottimizzazione e l'altro per la gestione delle scorte, potrebbe sembrare superfluo. Abbiamo però constatato che, trattandosi di due operazioni distinte, è in realtà una mossa vincente. Per ulteriori dettagli, consulta la nostra pagina dedicata al
controllo delle scorte.
Rapporto con i quantili del punto di riordino
La previsione con metodo quantilico offre la possibilità di eseguire un calcolo statistico diretto dei
punti di riordino. Nel caso del metodo Min/Max, quando si rende necessario un riordino, sia il valore Min che il valore Max dovrebbero essere aggiornati e fatti corrispondere al valore del punto di riordino indicato dalla previsione quantilica.
Lasciare invece i due valori inalterati porterebbe, in pratica, a emettere un nuovo ordine a ogni unità di prodotto venduta. In realtà, però, se escludiamo i casi di drop shipping, gli ordini non vengono emessi non appena viene ricevuta la richiesta del cliente, ma secondo una programmazione ben precisa.
Se quindi gli ordini vengono emessi secondo un preciso calendario, nei giorni in cui non sono previsti riordini per nessuna delle SKU i valori Min e Max dovranno essere azzerati. In questo caso, i dati relativi al calendario di riordino saranno integrati direttamente nelle previsioni quantiliche, attraverso un lead time prestabilito.