By Estelle Vermorel, February 2020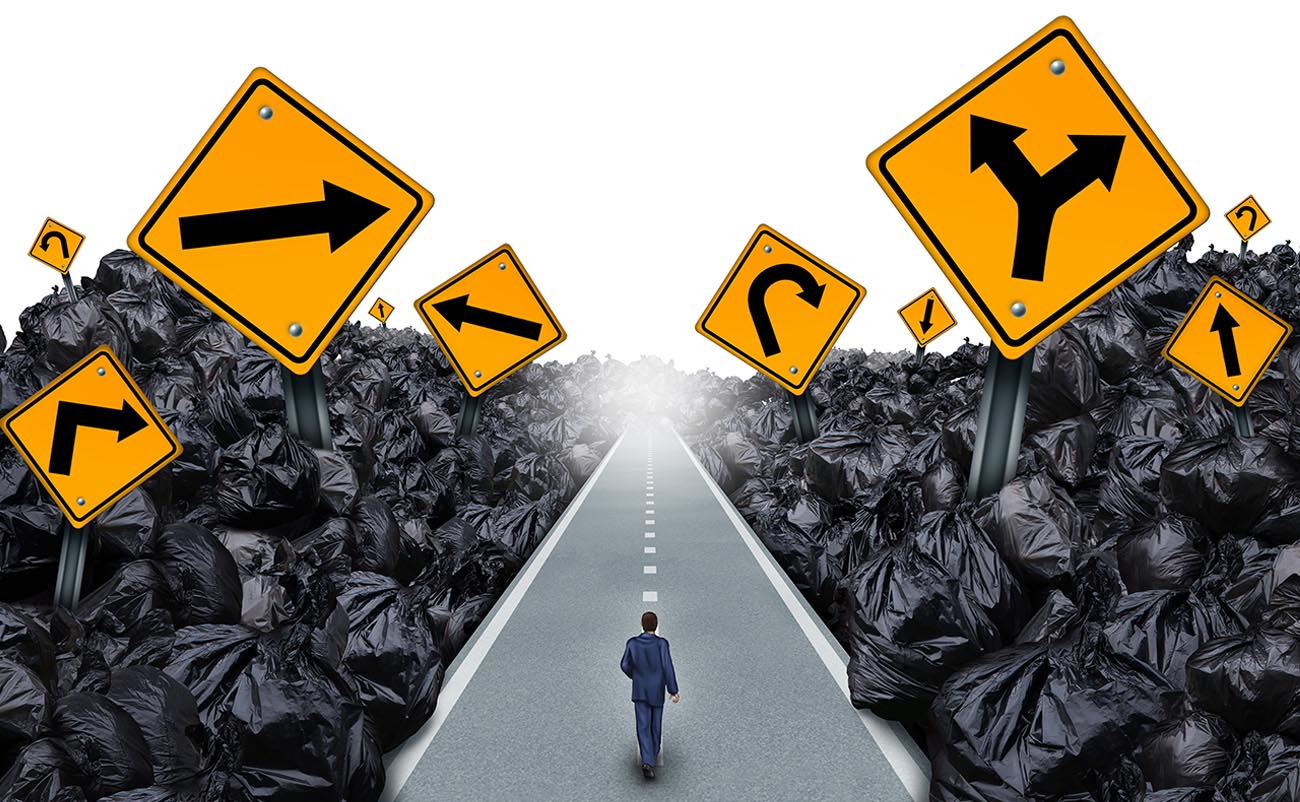
Since the 90’s, “lean” has been an important concept, in the world of manufacturing first, and, from there, in other fields such as Supply Chain Management (SCM). What does it mean for a supply chain to be lean? What comes with the continuous effort to reduce waste? Given the complexity and multi-dimensional aspect of SCM, and the trade-offs that are made every step of the way to cope with the multiple options related to a supply chain network, not to mention the fluctuations of demand or lead times, Lean SCM sounds more like an unreachable utopia than anything else. However, this perspective can be key to restructuring supply chains in a more efficient and competitive way - albeit with some noticeable twists compared to the original Lean Manufacturing vision.
From Lean Manufacturing to Lean Supply Chain Management
Without engaging in a full description of Lean Manufacturing, here is a very brief reminder of the essentials. Lean Manufacturing refers to a method meant to minimize waste and reduce costs and production time, inspired by the Japanese automotive manufacturer Toyota, and made popular under the term “lean” in the 90’s. In particular, it implies
the reduction of 3 types of waste - in Japanese,
muda,
mura and
muri - that is, 1) processes or activities that don’t add value (e.g. overproducing or moving items unnecessarily), 2) unevenness (e.g. uneven schedules, idle periods followed by rushes) and 3) overburden (e.g. overburdened workers with too heavy weights or equipped with the wrong kind of tools, or teams or machines pushed beyond reasonable limits). An extension of the Lean Manufacturing approach also implies creating smooth flows in the production and reducing bottlenecks.
More than tools, Lean Manufacturing relies on
a cultural and managerial approach, with a strategy, procedures, standardization and simplification designed and implemented by a leadership whose goal is continuous improvement, keeping in mind the respect for people. Therefore, a lot of emphasis is placed on the long term relationship that should be maintained with employees, the communication of the lean philosophy to the workers, and the essential link between veterans and newcomers (
Senpai and
Kohai in Japanese), etc. The employees’ adherence to - and indeed the belief in - the reduction of waste and continuous improvement goal is instrumental to the success of a Lean Manufacturing initiative, and probably the reason why they’ve been harder to implement in Western cultures. This is also the reason why Lean Manufacturing has been
sometimes described as a religion rather than a science.From there, the initial concept has been transposed to supply chains and supply chain management. A “lean” SCM also aims at eliminating waste by applying continuous efforts to get
better inventory control and streamline all the steps of a supply chain, not only manufacturing but also warehousing, transportation, returns, etc. There lies the issue: SCM is by nature extremely complex and involves different activities, teams, flows, neverending lists of options at every turn, driven by the need to adapt to a potentially very fluctuating and hard to forecast demand (for more details, see
Supply Chain Management (SCM)). Nevertheless, the continuous improvement goal and track for waste remains valid, but it should be adapted to such complexity and therefore cannot rely solely on cultural and managerial measures.
Eliminating waste in Lean Supply Chain Management: holistic perspective vs. local
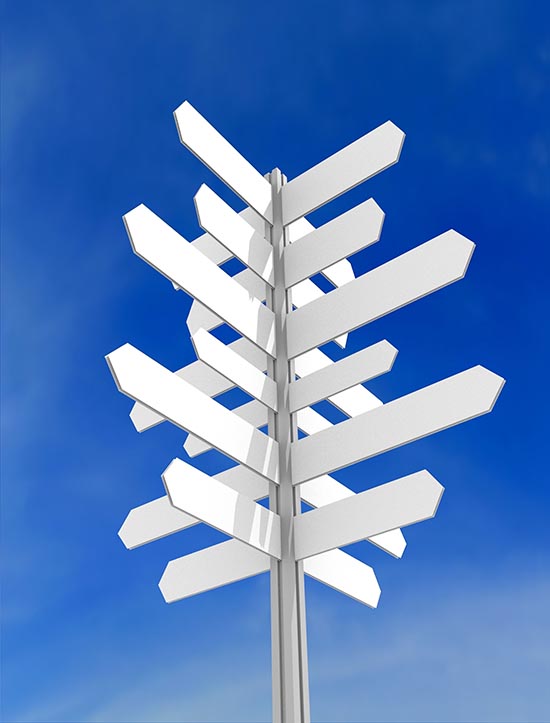
The complexity of Supply Chain Management comes from the fact that it is all-encompassing. More than that, supply chains are replete with conflicting points of view, processes, incentives and even conflicting electronic records. As a consequence, a holistic perspective is essential for any kind of initiative meant to improve a supply chain.
Let’s take the example of a company with a retail network. The goals - and quite possibly the financial incentives - of the procurement team in charge of a central warehouse is not always aligned with the goal of the store managers/owners. The central procurement might want to reduce inventory while each store manager simply wants to make sure their particular point of sales is replete with products, with no stock outs to never miss a sale - especially if unsold items can be returned to the central warehouse and if the store itself doesn’t bear the costs related to overstock. The store managers will even tend to reverse engineer the central warehouse’s logic, knowing that if a product starts to sell well, it’s going to soon be out of stock at the warehouse level, therefore they should order in large quantities as soon as the sales seem to pick up. By doing that, not only do they risk being overstocked, they will also monopolize products that could have been sold faster in other stores and they will create stockouts elsewhere. The situation can even be worsened if misalignments appear in the electronic records within the network, creating false impressions of stock outs. What should the answer to that be? What does “lean” mean in such a context? Making things smoother for the store manager would mean making sure he is never out of stock and can easily return products, but making things smoother at the warehouse level could on the contrary mean sacrificing the performance of certain stores for the sake of others with a faster rotation. At the same time, promoting only faster rotating stores will be damaging in the long term for the retail network, as some stores’ performance might drop drastically.
In Lean Manufacturing, the challenges tend to be of a more binary nature. Manufacturing has to deal with physics, which is pretty hard, but at least it either works or it doesn’t. There is of course always a matter of balance and fine-tuning, but as a rule of thumb, making step A, then step B, and C of the manufacturing process leaner tends to make the production leaner as a whole. Not so much with supply chains. A leaner step B could actually create problems for step C.
The Lean SCM is not the implementation of local improvements, but should always adopt a holistic perspective. One aspect is the alignment of incentives, whenever doable - this is not always the case, as it is certainly hard to give incentives to individuals on the performance of the company or supply chain as a whole. Another aspect would be the alignment of IT systems (more on that later), but most of all, there is the very important (and thorny) matter of KPIs. If a Lean SCM is meant to reduce waste, how do you measure it? Better, how do you measure it with a holistic perspective, as it is always possible to produce dashboards overflowing with KPIs specifically adapted for every aspect of every task.
But how do you choose KPIs and metrics that are going to make sense at every level?The answer is in fact pretty simple and very seldom applied in practice: dollars/euros or any currency that makes sense for the company are the best illustration for the reduction of waste. It means that
every action taken in the course of a Lean Supply Chain initiative should be seen through the prism of its financial impact and return on investment and actions should be compared, weighed and prioritized accordingly. If keeping product A in the central warehouse means 100€ of inventory costs + 1000€ of potential lost sales for stores A and B, but a potential gain of 2000€ for store C, then the answer is pretty obvious: moving products to stores A and B is a waste. Of course, this is the overly simplified version. On the one hand, lost linked sales or loss of other products to product A and loss of loyalty overtime should be placed in the balance, as well as delivery costs increasing for products B and C if the truck is not filled anymore for stores A and B, and on the other hand potential cannibalization of other products by product A not being out of stock in store C, and so on and so forth. To top it all off, this is all based on potential sales, by nature uncertain, which also needs to be taken into account...
The complexity can quickly become staggering, but it is unavoidable given the nature of SCM. This is also where Lean SCM can differ from Lean Manufacturing. The challenge cannot be considered as mainly solvable through a managerial approach, mainly oriented towards the relation to the workforce within the supply chain. Simply because solving the problem of waste reduction within a supply chain goes way beyond what the human brain can do on its own. SCM is multi-dimensional and so is the way to Lean SCM: it implies IT, tools, change management for the teams and accepting the fact that simplicity is not always preferable.
What are the changes brought by Lean Supply Chain Management?
Simple vs. simplistic
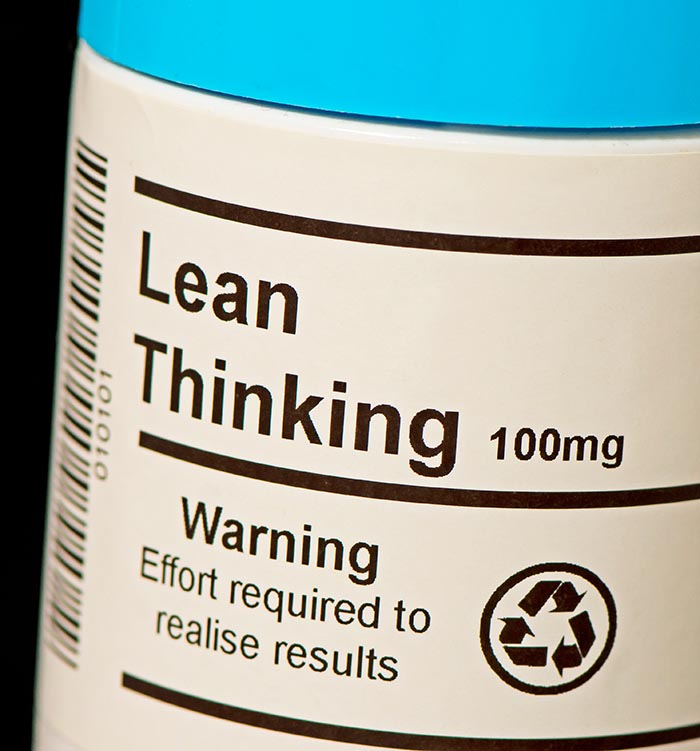
A Lean Supply Chain Management initiative can be expected to bring changes on multiple levels and is by no means an easy task. Such initiatives will require
strong leadership, and strategic thinking at the highest level - this is also the case for Lean Manufacturing. One singular difference with Lean Manufacturing though: the leaders of such initiatives need to accept and keep in mind that simplistic models are frequently adverse when it comes to Lean SCM. Seeking simplicity - which is always good - should not dismiss real-world irreducible complexities..
For instance, there can be several ways to procure the products distributed to the customers, and sometimes procurement is performed by different individuals or even different teams for the same product - one ordering routinely in small or medium quantities, the other getting infrequent opportunities of large bulk orders at very low costs that are going to unbalance the inventory of a given product, not to mention cannibalize several others. The easy answer in order to reduce unevenness would be reducing the number of suppliers, the types of contracts, the pricing conditions, etc. In turn, it would also mean less flexibility, no possibility to balance oversea vs. local suppliers, or to play supplier lead times and pricing conditions against one another, or to keep “backup” suppliers, which could be very beneficial for the supply chain as a whole in terms of costs, customer satisfaction, etc.
Again, SCM is a game of trade-offs, and it’s about being weighing options against one another, ideally being able to choose at the last minute in order to reduce uncertainty. It can mean being able to afford quick replenishments for products that have been selling better than expected. This can be done with local assembly for instance, such as being able to print patterns locally on raw materials that have already been sourced and bought in advance at a low cost, rather than ordering directly the finished goods by containers from China with unavoidable long term planning due to production and transportation delays. In such cases, Lean SCM would mean accepting the multiple processes and suppliers, coordinating them and providing the tools to quickly assess the performance of one option against another, thus enhancing the capacity of procurement to react quickly to demand. Always looking for simplicity is not a viable option for Lean SCM, as it often means choosing a local improvement over the general perspective.
Less isolation, more coordination
Complexity is part of the supply chain package and there is no avoiding it. What it also implies is the need for strong coordination in order to achieve a leaner supply chain. The barriers that have been created over time between every stage of a supply chain - and indeed every team - need to be lowered, at least partially, in order to allow for a better understanding of the whole. This is where the involvement of the teams is key. For a proper Lean SCM initiative to be implemented, the business processes, the tools and IT systems used should be understood, discussed and documented. It is impossible to make everything transparent with the highest level of detail for every member of the organization, but there should be understanding and transparency, as much as possible, for at least several
key coordinators in charge of the project and representing their departments. Those individuals would be in turn in charge of relaying the initiative to the rest of their teams.
Documentation is key for the success of such a process. In general, change management is an important step for a successful Lean initiative, as it often comes with a certain restructuring of the workforce.
Less isolation can have repercussions on IT - it doesn’t mean that everything should be merged in one big fit-them-all program, simply that they should talk to each other more efficiently - it can also have repercussions on the way the organization operates financially. Local improvements are the pitfalls of Lean SCM, and one typical illustration of such a pitfall is the optimization of local budgets. It doesn’t mean that budgets ought to disappear entirely, but more flexibility should be allowed, and unnecessary barriers should fall entirely, in particular for procurement. Yes, separated budgets are easier to handle, but the money spent is always the company’s money, so why not spend it in the best way for the whole, rather than to risk overspending on some categories of products and cutting the budget elsewhere where the ROI would have been better? Reduction of waste should be applied at the whole catalog level for an organization, not category by category, or for team A vs. team B.
Increasing white collar productivity
In particular, the goal of Lean SCM initiative should be to
obtain the same kind of gains in terms of efficiency and productivity that were obtained in Lean Manufacturing for the blue collar workforce. These gains have yet to be made in the vast majority of supply chains for white collars. There are more and more people toying with Excel spreadsheets or the likes, with time-consuming and repetitive tasks in a pretty unstructured way - not to mention the shadow IT that usually accompanies these kinds of activities. It can stem from the development of an internal bureaucracy with more and more complex processes, multiple steps of validation (usually related to waterfall plan structures), or from legacy IT systems. The result is typically an overburdened workforce with ever increasing numbers, a lack of transparency (shadow IT, or individually customized Excel spreadsheets with undocumented rules being the perfect example), a lack of structure and standardization, and short term views as there are no general perspectives or relevant KPIs to orient the decisions. As always, with supply chains, the more the market pushes you toward more options (product customization, last minute deliveries, etc.) the more the burden for these white collars, all of it getting in the way of flexibility and the ability to choose easily between options in order to reach the best trade-off possible.
While production has been the object of a lot of attention and refinement in a bid for higher productivity and lower costs,
the potential for improvement of the planning, pricing and scheduling is huge. One of the impacts of a lean SCM is to enhance the efficiency of the personnel in charge of such tasks, giving them the structure they need to make faster and better decisions for the organization as a whole, and possibly
automating part of the routine that has no added value. Often it means reducing the teams, or reorienting their activities toward tasks with higher value that cannot be automated.
It also means
getting rid of old habits and legacy processes. For instance, the typical buffers such as
safety stocks, or oversimplified ways of thinking such as
Min/Max orders are the first kinds of waste to be targeted. All of this naturally implies change management and again should be led at the higher level and trickled down to the end users, as their adherence to the new processes is key for the success of any initiative of this nature.
Dedicated investments
As stated earlier, SCM is extremely complex and any kind of effort to reduce waste means measures and financial assessments of all possible options.The understanding of business processes should be backed by the analysis of proper data to make sure the demand, the trends, and the impact of strategies are measured and quantified. Therefore, tools are not only necessary, they are unavoidable. Herein also lies the difference with Lean Manufacturing. If SCM is the science of trade-offs, Lean SCM should remain strongly anchored in facts and not be based mainly on belief.
However, since every supply chain is unique, with its own set of constraints, processes, specificities - and legacy - aiming for Lean SCM usually implies dedicated investments, as
there are no ready-to-use tools on the market. Such tools should be able to adapt to the specific set of constraints of a given supply chain, in order to assess its performance with as broad a perspective as possible, they should be able to take in inputs from different IT systems if needed. Ideally, a Lean initiative can also imply the creation of a system to gather all the data, namely a data lake. This would be the basis to any further initiatives to optimize the supply chain. Alternatively, IT can also be restructured in a leaner way.
In this regard, it should be emphasized that
Simple and Easy are two different things. Legacy exists for IT the same way it exists for old habits and processes within a team. There is a lot of accidental complexity attached to IT systems in supply chains. More often than not, counting units is not coherent from one side of a supply chain to the other, the naming conventions vary from one system to another with heterogeneous semantics. As an example, the fields including dates are usually a nightmare: within the same table and indeed the same column, from one line to the other a date can be an order date or a date of return… The easy way, often used in companies, consists of patching the systems in an incremental way, adding a new column here and there, or reusing already existing columns in a different way (probably the reason why returns appear in the same column as orders). To make things lean, the system should remain simple in a structural way: one type of event equals one table, with an appropriate and explicit name, ideally properly documented somewhere as to the content of said table. It means that when a supply chain evolves IT should be deeply revisited to avoid legacy. To go back to the 3 types of waste, IT structural issues can cause unevenness (e.g. lack of coherence from one table to the next, or within systems), tasks without added value (e.g. workarounds performed by the staff to compensate for the issues) and ultimately overburden (e.g. staff overbooked by said meaningless tasks or whose productivity is drastically reduced).
When it comes to modern supply chains, IT is - or should be - at the very center of any Lean efforts.Lokad’s take on Lean Supply Chain Management
Lokad’s
Quantitative Supply Chain has a lot in common with the Lean philosophy. Definitely, the reduction of waste - in particular through better inventory control - is a goal we share. We also always try to keep in mind a holistic vision, based on proper KPIs. For Lokad, a Quantitative Supply Chain initiative should be led in a transversal way, with the help of project coordinators for a deep understanding of the business process, but with quantitative assessment through advanced data analyses.
Muda (actions that do not add value) should result in automation, and the delivery of a system to support procurement, planning or pricing teams so they can make decisions faster in a more efficient way. When it comes to forecasting, it also means forecasting directly at a level that makes sense business wise, not with conventional aggregations or unuseful precisions (e.g. forecasts day by day if orders are placed only once per month), or to satisfy buffers (such as safety stocks) that are mainly legacy practices.
Mura (unevenness) should be tackled in particular through the study of the data, with a detailed mapping at the very beginning of any implementation, in order to provide a strong basis for any further analysis. Finally
Muri (overburden) is strongly related to automation and support for the teams by expert Supply Chain Scientists, so that the teams are not left to manually handle catalogs of thousands, if not hundreds of thousands, of references. It also means making sure inventory remains in control: warehouses or stores are not overflowing with excess amounts.
Through
Envision, we adopt a flexible approach to perform probabilistic analyses of all options available, assessing their financial impact and offering the end users the possibility, through dashboards, prioritized lists (purchase orders lists, dispatch lists, discounts, …) and KPIs, the possibility to automate some of their actions and to perform simulations and react quickly to the market.